'바다 위 건축' 혁신 이끄는 현대건설
-
기사 스크랩
-
공유
-
댓글
-
클린뷰
-
프린트
'공장형 케이슨 공법' 최초 개발
공사기간, 절반 수준으로 단축
인천신항 부두공사 현장에 적용
국내 최대규모 케이슨 제작·설치
공사기간, 절반 수준으로 단축
인천신항 부두공사 현장에 적용
국내 최대규모 케이슨 제작·설치
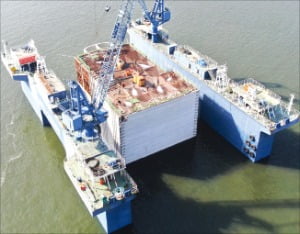
이번 컨테이너부두 하부공 축조공사에 사용되는 케이슨은 높이 27m에 폭과 길이가 각각 25m, 43m에 달한다. 1함당 무게는 1만1000t이다. 속이 빈 커다란 콘크리트 구조물인 케이슨은 바다에 가라앉혀 항만 안벽의 본체나 방파제 등으로 사용된다.
케이슨 공법의 선두 주자로 꼽히는 현대건설은 세계 처음으로 ‘공장형 슬립폼 공법’을 개발했다. 건설사의 슬립폼(활동식 거푸집) 공법과 조선업계의 중량물 이동 기술을 결합해 육상 소규모 부지에서 다량의 케이슨을 만들어내는 시스템이다. 자동차 생산라인처럼 컨베이어벨트를 활용해 ‘바닥판 만들기→벽체 세우기→콘크리트 양생→플로팅 도크에 선적’ 등 4단계 제작 공정을 차례로 진행한다.
공장형 슬립폼 공법이 개발되기 전에는 바다에 인접한 곳에 매우 넓은 케이슨 제작 부지가 필요했다. 과거 플로팅 도크나 대형 바지선 위에서 케이슨을 제작하는 방법이 주로 이용돼 왔다. 하지만 협소한 장소로 인해 생산성이 떨어질 수밖에 없었다. 공장형 케이슨 공법이 도입된 후 공기가 기존보다 50% 이상 단축됐다는 게 현대건설의 설명이다. 현대건설은 인천신항 공사 현장에서 30㎞ 떨어진 곳에서 1주일에 케이슨 1함을 만들고 있다.
육상에서 제작된 케이슨은 플로팅 도크에 실려 바다 한가운데 진수장으로 옮겨진다. 플로팅 도크에 물을 채워 가라앉으면 케이슨은 부력에 의해 뜨게 된다. 이때 예인선을 이용해 케이슨을 정해진 위치로 끌어낸 뒤 바지선을 이용해 바닷속에 영구적으로 설치한다. 현장 관계자는 “옆 케이슨과 10㎝ 이하로 떨어진 위치에 새 케이슨을 설치한 뒤 빈틈을 메운다”며 “각도가 조금이라도 뒤틀리면 안 되기 때문에 설치 과정에서 고도의 정밀함이 필요하다”고 말했다. 이번 공사 현장에선 케이슨 42함을 심어 총 1050m 길이의 항만 터미널 안벽을 세운다. 현재까지 29함 설치가 완료됐다.
부산신항과 울산항 동방파제, 강원 삼척 생산기지 부두, 인천항 국제여객부두 2단계 등에도 현대건설의 케이슨 공법이 사용됐다. 현대건설은 리비아 태국 싱가포르 등 해외에서도 800함이 넘는 케이슨을 시공했다. 2018년 수주한 싱가포르 투아스 핑거3 프로젝트에선 227함의 케이슨을 설치해 싱가포르 국토의 7%를 확장했다.
선박 대형화 등 추세에 따라 케이슨 공법의 중요성은 더 커질 전망이다. 업계에서는 당장 2억1600만㎡ 규모의 해상 매립이 예정된 부산 가덕도 신공항 공사에도 케이슨 공법이 핵심 기술로 활용될 것으로 예상한다.
■ 케이슨
수중 시설물 작업을 위해 만드는 속이 빈 대형 콘크리트 구조물. 육상에서 속이 빈 상자 형태로 케이슨을 제작한 뒤 해상으로 옮겨 바다에 통째로 가라앉히고 흙과 모래로 속을 채워 항만의 안벽이나 방파제 등으로 사용한다.
인천=이인혁 기자 twopeople@hankyung.com